- What Are Common Causes of .TIG Files Lost or Failure?
- How to recover lost .TIG files?
- Programs to recover .TIG files
- How to open file with .TIG extension?
What Are Common Causes of ".TIG" Files Lost or Failure?
There are several common causes of ".TIG" (Tiger) files lost or failure. Some of them include:
- Accidental deletion: Users may accidentally delete ".TIG" files while organizing or cleaning up their computer's storage. This can lead to the loss of important files.
- File system corruption: If the file system on the storage device containing ".TIG" files gets corrupted, it can result in file loss or failure. This can happen due to power outages, improper system shutdown, or hardware issues.
- Virus or malware attack: A computer virus or malware infection can corrupt or delete ".TIG" files, causing them to become inaccessible or fail to open.
- Software or hardware malfunction: Issues with software or hardware components, such as a faulty hard drive or a software bug, can lead to ".TIG" file loss or failure.
- Operating system errors: Errors or glitches in the operating system can cause ".TIG" files to become corrupted or lost. This can occur due to software conflicts, system crashes, or improper system updates.
- Human error: Human mistakes, such as accidental formatting of a storage device containing ".TIG" files or improper handling of files, can result in file loss or failure.
- Physical damage: Physical damage to the storage device, such as a hard drive failure or damage due to water or fire, can lead to the loss of ".TIG" files.
It is important to regularly back up important ".TIG" files to prevent data loss and use reliable data recovery tools or services in case of file failure or loss.
How to recover lost ".TIG" files?
Sometimes while working with a computer, laptop or other stationary or mobile devices, you may encounter various bugs, freezes, hardware or software failures, even in spite of regular updates and junk cleaning. As a result, an important ".TIG" file may be deleted.
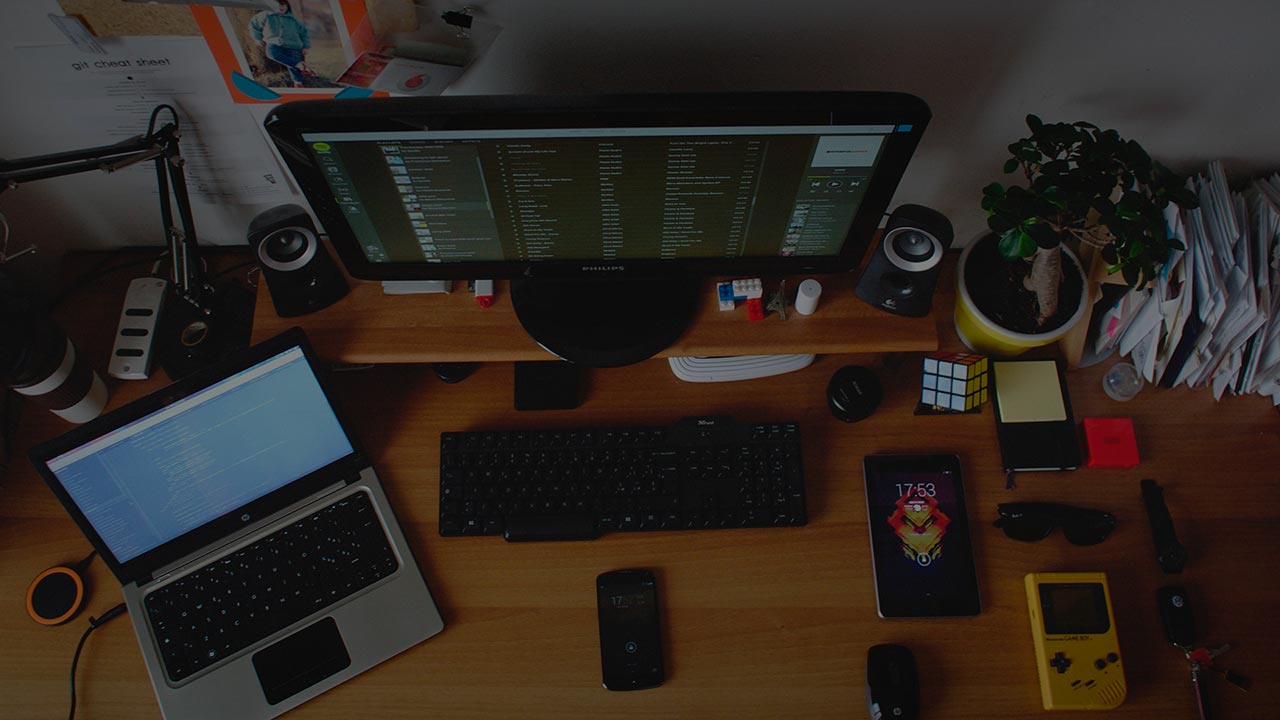
🧺 How to Recover Files and Folders After Sending Them to the Recycle Bin and Deleting? (Windows 11)
By no means should you think that the only way to recover a ".TIG" file is always to create it once more.
Use programs for recovering ".TIG" files if a file was lost after accidental or deliberate deleting, formatting the memory card or the internal storage, cleaning the storage device, after a virus attack or a system failure.
Programs to recover ".TIG" files
Looking for a way to get files back? In cases when files were deleted and they cannot be restored by using standard operating system tools, use Hetman Partition Recovery.
Follow the directions below:
-
Download Hetman Partition Recovery, install and start the program.
-
The program will automatically scan the computer and display all hard disks and removable drives connected to it, as well as physical and local disks.
-
Double-click on the disk from which you need to recover ".TIG" files, and select analysis type.
-
When the scanning is over, you will be shown the files for recovery.
-
To find a file you need, use the program’s interface to open the folder it was deleted from, or go to the folder "Content-Aware Analysis" and select the required file type.
-
Select the files you have been looking for and click "Recovery".
-
Choose one of the methods for saving the files and recover them.
How to open file with ".TIG" extension?
Looking for how to open a stereo tI Connect Backup File image file file?
Programs that open ".TIG" files
Windows |
---|
![]() |
![]() |
Mac |
![]() |
![]() |
Additional Information
-
File type: TI Connect Backup File
-
File extension: .TIG
-
Developer: Texas Instruments
-
Category: Backup Files
-
Format: Binary